( 1 ) Four factors that affect the reproducibility of graphite furnace analysis. The pretreatment of the sample is completely incomplete.
2 Is the temperature setting procedure reasonable and unreasonable?
3 Is it appropriate to adjust the injector?
4 Is the performance of the graphite tube intact?
( 2 ) Influencing factors of graphite tube 1 In summary, the performance and state of the graphite tube directly affect the reproducibility of the sample test; corresponding to the instrument of a certain model, the graphite tube used is not only the outer dimensions It must be consistent, and its resistance R should be consistent (the resistance of the graphite tube used in the Z-2000 original suction is 30 milliohms). This is because the graphite furnace power supply is generally a constant current source power supply mode. That is to say, once a certain temperature program is fixed, the power supply current I of the graphite furnace is correspondingly changed, so the graphite tube thermal power P=I2× R; It can be seen from the formula that the change of the resistance value R of the graphite tube directly affects the thermal power P. When the graphite tube is used for a certain number of times, the wall of the tube becomes thinner and the resistance increases, and the inner and outer walls of the tube produce a "honeycomb"-like physical change (see Figure-1); at this time, the temperature generated by the graphite tube is much higher than the original Set value; when this happens, the biggest unfavorable factor is: the actual temperature of the graphite tube in the ashing stage is higher than the original set temperature, and some low temperature elements (such as Pb, Cd, etc.) tend to cause at this stage. The “ashing loss†causes the absorbance to drop, which is the most common and most overlooked fault in the analysis of graphite furnaces. In addition, since the inner tube wall is honeycomb-shaped, the sample is easily immersed in the deep part of the tube after injection, and the coexisting material and the element to be tested are not easily burned or dissociated completely during the ashing, atomization, and scavenging stages, thereby generating a memory effect. .
Figure - 1
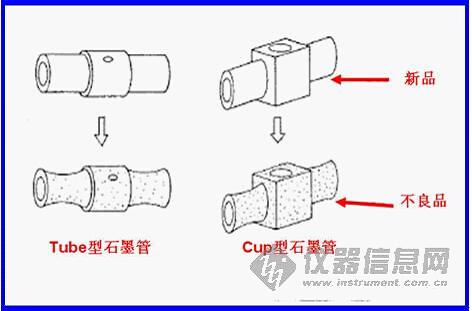
Figure - 2
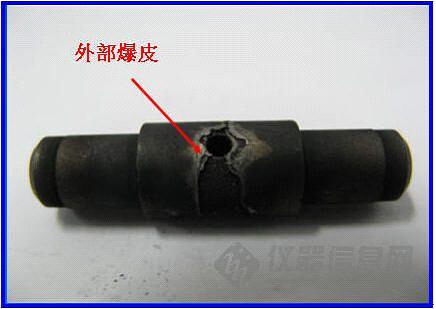
Figure - 3
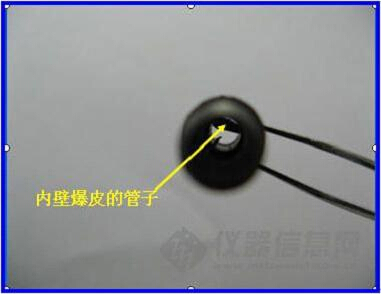
Figure - 4
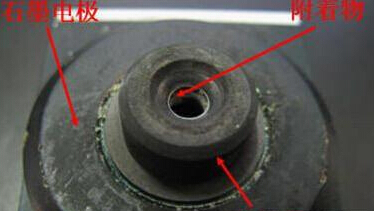
the way is:
1 Remove the contaminated graphite ring together with the graphite electrode. Note that the graphite ring cannot be removed separately; since the graphite ring can not be removed once it is removed from the electrode, the graphite ring is in contact with the electrode after the secondary loading. Poor contact occurs and the contact surface is ignited (the heating current is too large).
2 Repeat the rubbing of the joint between the graphite ring and the graphite tube with an ethanol swab.
3 Find a complete old graphite tube at one end (of course, the new tube is best), hold one end of the graphite tube with your thumb and forefinger, place the entire other end vertically into the graphite ring, and make the fingers move back and forth (similar to the drill Fire-like) until the graphite ring interface is bright (see Figure-5)
4 Finally, use an ethanol swab to repeatedly clean the polished part of the graphite ring.
The above cleaning method is equally applicable to other structurally similar atomic absorption instruments.
Figure - 5
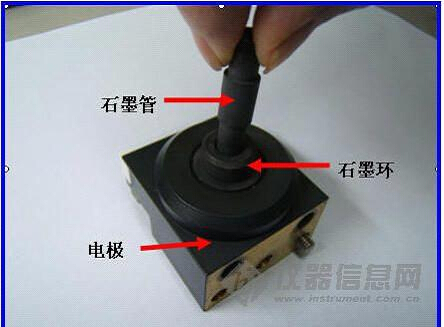
Figure - 6
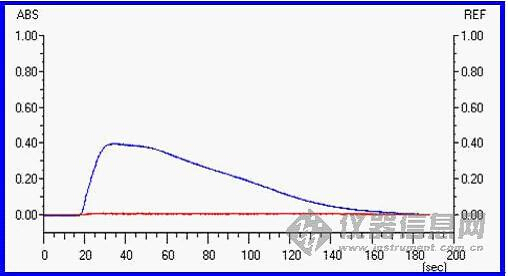
1 Graphite electrode leaks from the inlet and outlet into the carrier gas pipeline due to poor sealing or improper installation. These traces of moisture are carried by the carrier gas to the inner wall of the graphite electrode. At the instant of atomization, the water is atomized. Rapidly low into water vapor and adsorbed on the quartz window (due to the low temperature of the quartz window) caused a false background absorption, and over time, the moisture attached to the quartz window was gradually evaporated, so the background The baseline returns to zero again. Judgment method: After the end of the cleaning phase, remove the quartz window and observe that there is no steam on the quartz plate. Solution: Replace the rubber seal at the bottom of the electrode or add raw tape. The appearance of the graphite furnace electrode and the quartz window is shown in Figure-7.
Figure - 7
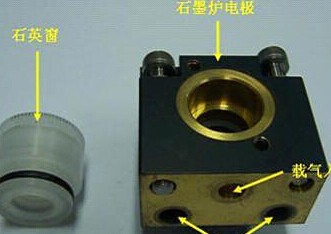
Figure - 8
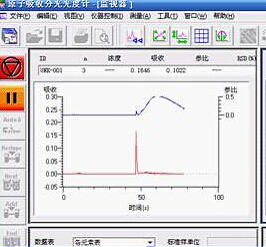
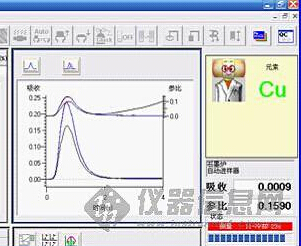
Figure 9 is an example photograph of the graphite furnace from the optical axis (the spot is illuminated in the lower right corner of the graphite ring).
Solution: Re-adjust the four horizontal screws of the graphite furnace platform. (Because the adjustment steps are more complicated, they will not be described in detail here)
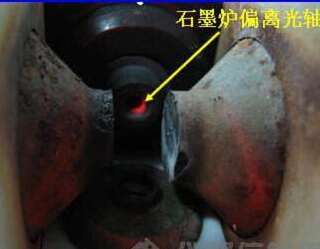
Shandong spring rain Water-saving Irrigation Equipment Co., Ltd., founded in 2011, located in Laiwu High-tech Zone, Jinan City. It is a high-tech enterprise focusing on innovative and efficient drip mold manufacturing and drip product development and production. After nearly ten years of innovation and development, now our company is the invisible champion enterprise in Shandong Province, and in a leading position in this field in China.
Our company people-oriented, build talent highland. At present, our company have 16 high, fine and advanced technical person, and cooperates with a number of scientific research institutes, forming a mold design, drip testing, flow rate testing and other professional technical personnel team. In recent years, we have obtained 3 invention patents, 33 utility model patents and 3 patent awards. In 2019, we were identified as an intellectual property advantage enterprise in Jinan city. We have undertaken 4 provincial science and technology innovation projects and won second prizes of Shandong Science and Technology Progress 2 times. Our company have built a drip mold engineering technology research center of jinan city, we have slow wire cutting machine, CNC machining center, precision EDM machine, 3D projection measuring instrument, CNC engraving, laser engraving and other advanced processing equipment. Mature technology and rich experience support the excellent quality of our company. Spring Rain pays attention to each link of production, implements 8S management, strictly controls the quality of products at the beginning, the middle and the end, and forms the seamless link of production and management. Our company have independently researched and developed flat drip molds with full hot runner, round drip molds with full hot runner and other products. With excellent quality, competitive price and good after-sales service, our company is well known at home and abroad, and has been sold well in Egypt, India, Iran, Turkey, Saudi Arabia, the United States and other countries
With the vision of "building a global professional drip mold supplier" and the mission of "providing solutions for efficient and innovative production of global water-saving irrigation enterprises", our company take "scientific and technological innovation to scale new heights; Keep improving, the pursuit of excellence; Honesty and trustworthiness, win-win cooperation "for the values of our enterprise. We try our best to make a positive contribution for the construction of water - saving and resource-saving society.
Inline Dripper Mould,Water-Saving Irrigation Equipment,Water Saving Equipment Of Emitter,Irrigation Products Mould
Shandong Spring Rain Water Saving Irrigation Equipment Co.,Ltd. , https://www.drippermould.com